車両の「位置情報」と「軌跡」を把握し、将来的に納期短縮を目指す導入事例
GPSを活用した動態管理によって、広大な工場の敷地内での「車両の位置把握」を実現。さらに運用していくなかで、「車両の軌跡」という新たな課題を発見し、潜在的なニーズを浮き彫りにしている。
-
1導入前の課題製造中の車両を広大な工場の敷地内から探す工数を削減したい
-
2導入の決め手目先の課題ではなく、本当に解決すべき課題を気づかせてくれた
-
3成果車両位置の特定にかかる時間が大幅に削減。さらに新たな改善点も浮き彫りに
-
4今後の展望納期の短縮を実現し、全国の工場でもスムーズな製造のために役立てたい
製造中の車両を広大な工場の敷地内から探す工数を削減したい
極東開発工業は、ダンプトラック・タンクローリー・ゴミ収集車など、特装車の製造における国内トップクラスのシェアを誇る総合メーカーです。建設、物流、環境という社会のあらゆるシーンで活躍する特装車。極東開発工業の名古屋工場では、豊富なラインナップを安定供給するために、Cariotが日々の製造ラインを支えています。
製造の流れとして、まずお客様から注文をいただきます。その後、トラックメーカーから運転席とフレーム、タイヤがついた「シャシー」と呼ばれるものをお預かりします。そのシャシーに対して当社で作った「ボデー」と呼ばれるダンプカーやタンクローリーを搭載して完成車にします。
シャシーが工場の敷地内のどこにあるのか、いつも自分の勘で探しに行くため、それがまったく違う場所に置いてあることもあります。ひとつのシャシーには設計・製造・検査などいろいろな部署の人が携わっているため、このような状況が発生します。みんなが自分の作業に応じてシャシーを移動するケースが発生し、思っていたところに車がないということが起きてしまいます。これは非常に生産性が悪く、無駄な工数だと常日頃から感じていましたので、車両の位置確認をスマホなどで瞬時に確認できないものかと考えていました。
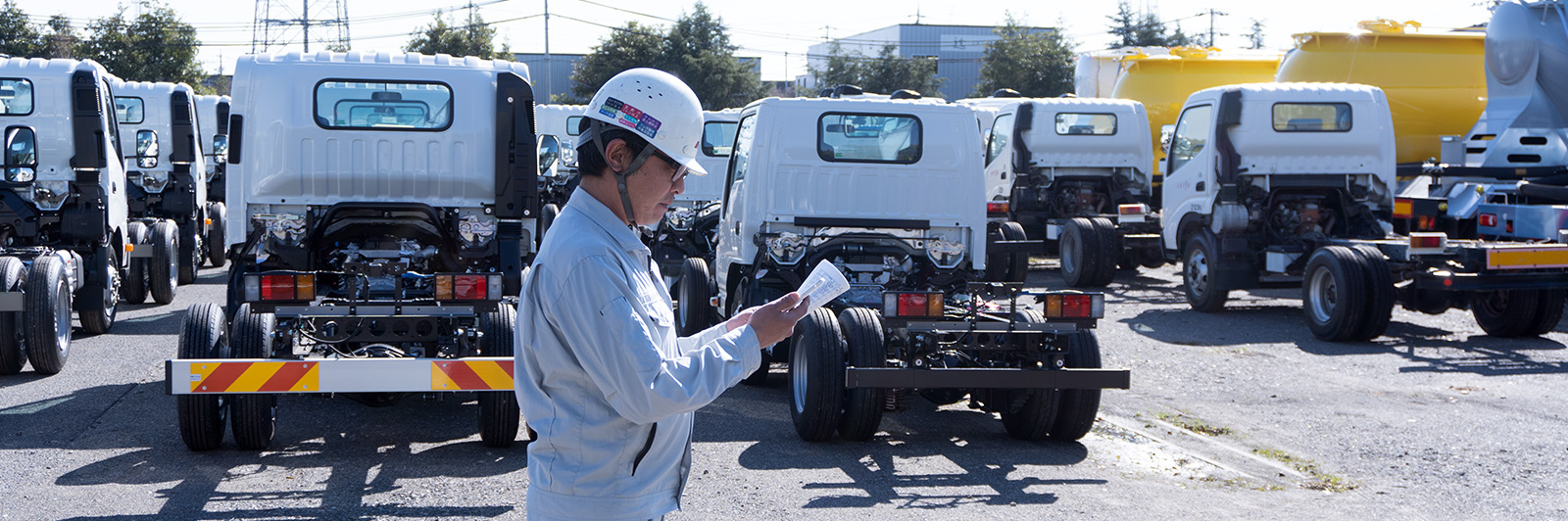
目先の課題ではなく、本当に解決すべき課題を気づかせてくれた
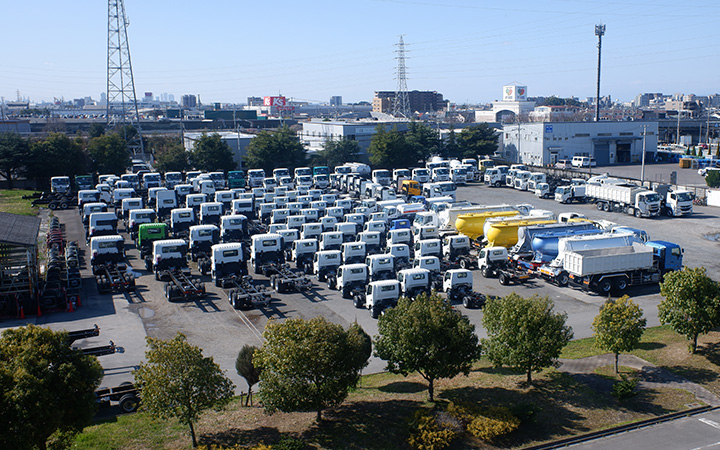
当社はマイカー通勤する従業員が非常に多く、免許証、車検証、保険証といった書類の管理が必要となります。特に、免許証などの有効期限はそれぞれ異なるので、各証書を最新情報に更新するための業務に多くの工数がかかっていました。何か良い方法はないかと思っていた矢先に、Cariotというサービスを知り、話を聞いてみたというのが最初のきっかけになります。
最初は車検証や免許証の管理について相談していたのですが、Cariotの営業担当者と打ち合わせをしていく中で、当社が本当に解決すべき課題は、工場内の車両位置の把握をとおして「製造工程における効率性・生産性を向上させる」ことであると気づきました。たしかに以前から工場内の車両の位置管理について課題があるとは感じていたものの、これといった打ち手がないままになっていました。
Cariotならばこの積年の課題の解決ができるのではないかと感じたことが導入の決め手です。
車両位置の特定にかかる時間が大幅に削減。さらに新たな改善点も浮き彫りに
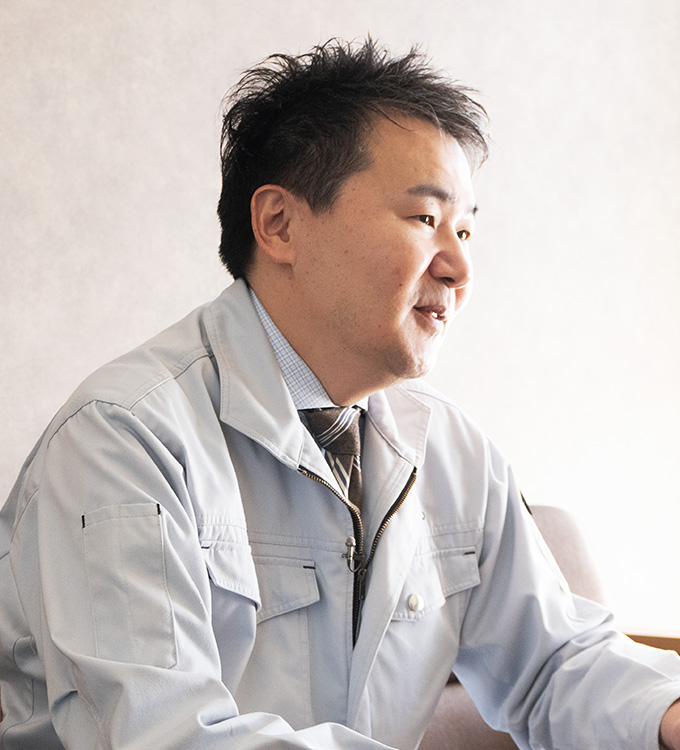
当社が抱えていた課題に対して対策を講じてみたことはありました。ひとつは車両を移動した人が位置情報をサーバーに履歴を手入力するという管理方法です。しかし、ヒューマンエラーがどうしても発生してしまいます。結果的に長続きしなくて、いつの間にかその運用は立ち消えになっていました。
Cariotを使ってみると、視覚的にどこに車両があるのかが瞬時にわかり、かつ位置情報は自動で取得されるので工数もかからない。導入してすぐに効果を実感することができました。
Cariotの営業担当の方と打ち合わせをしていくなかで、すでに明確になっている課題に対してだけでなく、まだわれわれが見えていなかった課題と改善策についても、さまざまな提案をいただきました。例えば、工場内にある車両がどんな動きをしているのかという軌跡も調べられるということを伺いました。
製造過程で車両を移動させる導線が効率的なのかどうか、今まで気にもしていませんでした。実際に使ってみると、A地点からB地点に真っ直ぐ動くだけでいいはずなのに、なぜかC地点を経由しているというデータを確認して、「これはなぜこっちに行くのだろう?」という疑問とあわせて、車を何回も切り返しをしているというデータも出てきました。わかったのは、車両を止める位置がすごく狭いところだったということ。止める位置を見直すことで無駄な走行や切り返しをなくし、スムーズな移動ができるようになりました。
当初の課題だけではなく、使っていくうちに新たな課題を発見して解決するということもできているので、非常に助かっています。
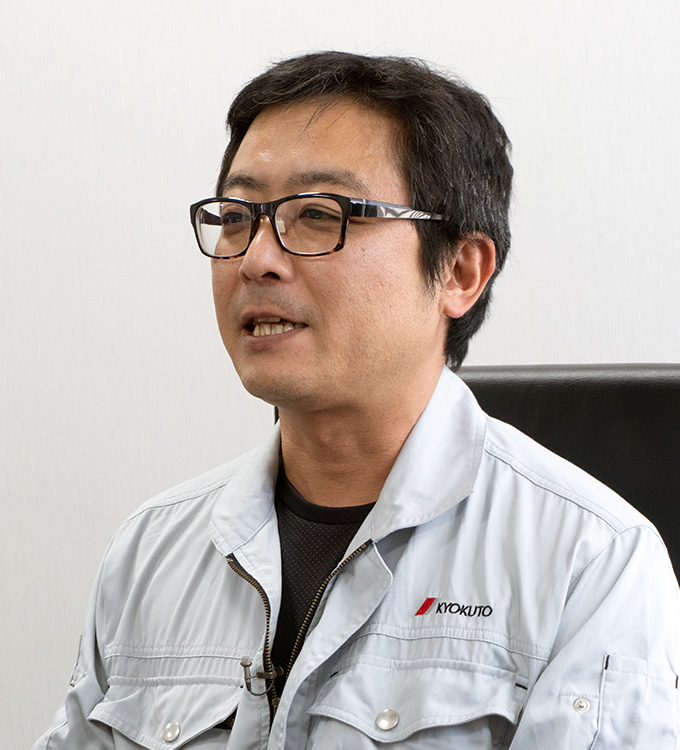
名古屋工場に20数年勤めているなかで、毎日のように工場内で車両を探し回っていました。工場内には約300台の車両があり、それらを探すために構内を歩くのはとても手間がかかる作業でした。他部署に電話をして確認したり、構内を歩いている人に確認したりして原始的な探し方をし、多い時は10~20分、時間がかかる時は30分以上も探し回っていることもありました。
でも、今はCariotのおかげで車両を探す手間が格段に減りました。スマートフォン慣れしている若い社員たちが扱いやすいシステムだと思いますし、私も普段見慣れているGoogle Mapを利用できるので、難なく使えています。
過去には違う車両をピックアップして間違った仕様の特装車にしてしまったというケースがありましたが、Cariotならそういった間違いを防止できるため、製造品質の維持・向上につながります。今後は工程管理のシステムと連動して、他部署との連携と改善活動などを進めていきたいです。
納期の短縮を実現し、全国の工場でもスムーズな製造のために役立てたい
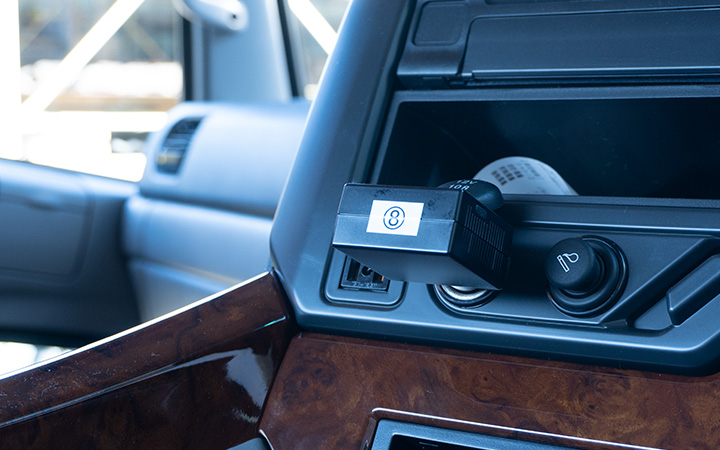
まずはCariotの運用の仕組みをしっかりと構築して、無駄な作業を一切減らすことを達成したいです。もちろんそれだけに留まらず、せっかくこのような便利なツールがあるので、Cariotで取得できるデータを利用して元々ある社内の工程管理システムと連動していくことを視野に入れています。さまざまなデータを一元管理して、工場全体でスムーズな製造を実現できればと考えています。
いま当社の製品はほぼオーダーメイドで製造する製品ばかりです。車両を探しにいく時間を縮めることで、次の製造工程の開始時刻を詰めることができる。それに伴い、さらに次の工程の開始時刻も詰めることができる。結果的に納期の短縮に繋がるのではないかと期待しています。
短縮時間としては1台あたり10分から15分くらいが目標です。現状は月間約200台の製造車両があり、1か月換算で約20時間の効果が出ればいいと考えています。Cariotの車両追跡システムがうまく軌道に乗れば、名古屋工場以外の全国の工場でも実用化して、当社全体の運用としてさらなる効果が出ると期待しています。
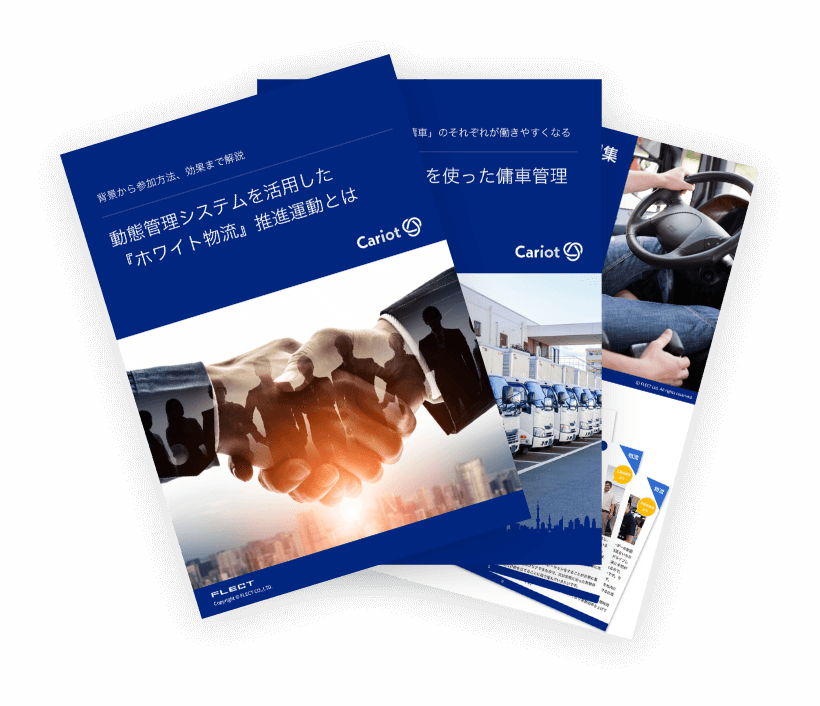